If--like me--you are not a professional kitchen designer, then designing the cabinet layout means:
- Editing your Houzz and Pinterest pages down to the most useful images.
- Cramming into your brain all the kitchen planning advice that time and your intellectual capacity allows.
- Putting all of your dreams and inspirations on the table (either physically or figuratively.)
- Knowing (or having a reference for) the cabinet companies' specification and sizes and all of your room dimensions, exactly. Absolutely, for sure, and accurately. And then...
- Figuring out the size and shape of every cabinet, panel and filler piece that will fit into the space while elegantly serving your needs and desires.
- Planning exactly how each part attaches to the parts around it. And then...
- Checking the total cost of all those pieces to be sure you are within your budget.
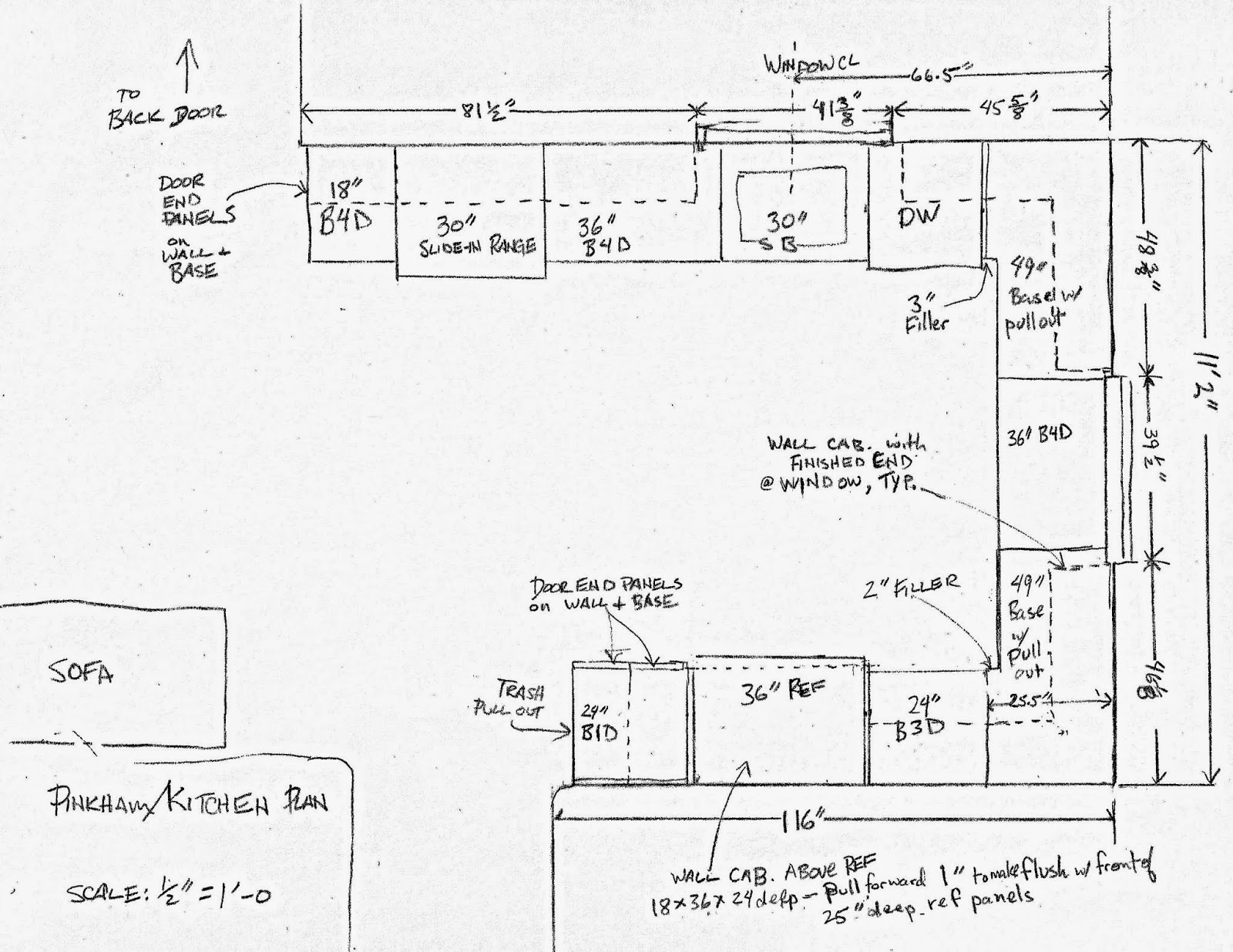 |
This drawing is here because it is useful; not because it is pretty. |
So. Yes. Know what you want. Know what is possible. Know what you can afford. And account for every eighth-inch and every dollar. Until that work is done, the design isn't. (
Or, go get some help.)
And then when it is "done," some flaw or potential improvement will wake you in the wee hours or hit you like a fog horn at midday, which will make you go back and revise, revise, revise. Maybe that is only me.
I began working on my design using Ikea's
Home Planner 3-D Tool, which is useful and yet far,far, far from perfect. After some hours of frustration, I tried a couple of other nifty CAD systems but there was not time for me to learn a new system before designing my kitchen. I went back to the system I've been using since age four: pencil and paper.
With those tools, a triangle, and my trusty plastic scale, I drew and drew ... until, a couple of months and many design changes and corrections later, I was ready to order Ikea cabinets, custom doors and additional alder lumber.
Inevitably, I went back and forth between Ikea's program and hand-drawing the floor plans and elevations. Their system is the most direct way to know you can buy the sizes and configurations you want because everything they sell for kitchens is available in the 3D Tool. When you have a design pretty well filled-in, copy it and take all the doors and drawer fronts off the cabinets in the copy design . The Item List function allows you to compare the costs of multiple plans. Talk about inspiration! Wait till you see how
cheap (
ahem) cost effective those boxes are after you take off the doors and drawer fronts!
BTW: I assume everyone knows that Ikea will do all of this work for you, if you want. They'll measure, design and install it all .
Go over and check it out if you'd like. They try to make it easy for you. (
Or, go get some help elsewhere.)
Which reminds me: If you're doing the design yourself, and also buying custom doors instead of theirs, you will
still want to sit down with an Ikea kitchen department person at the store so they can check over your design in their Planner system. They will make sure you have not done something stupid, something that would stop your cabinet installation in its tracks, like thinking you could jam two cabinets into a corner with no fillers.
As I said, Ikea people want to sell their products, and so they really won't be offended if you are doing a hybrid kitchen with custom doors. They only want you to buy their products, not live inside one of their catalogs In fact, they might even admire your pluck and creativity. They might quietly ask you where you're getting those custom doors because they, too, wouldn't want any of Ikea's doors in their kitchen. They might. Not every Ikea employee drinks the Kool-Aid, you know.